粉末冶金产品的密度问题
粉末冶金运用粉末颗粒压制而成,粉末颗粒与颗粒之间本身就有着间隙,所以在密度这方面不如熔铸,但是对于密度要求不需要那么高的量产件上,粉末冶金优势就会体现出来,尤其是需要自己润滑作用或是有透气率要求的零部件,比如轴承、空气监测器。通常压制粉末冶金密度高到7.3左右。如果在密度上有特殊要求,连云港东睦新材料有限公司同时拥有MIM注射成形技术,MIM注射成型就可以制造高密度的量产件。但是常规粉末冶金使用还是占粉末冶金行业的大头,能够决定产品密度的因素有很多,最直观的就是压制的过程。
在压制过程中,压力增大粉末冶金产品的密度就会越大,粉末在受到压力作用下会发生位移和变形,这个过程基本分为三步。
由粉末颗粒之间有间隙,在刚施加压力的过程中,粉末颗粒会紧密贴合在一起,使颗粒之间的空隙迅速减小,这个过程中是密度增长最快的阶段,我们称为压缩粉末颗粒间隙阶段。第二阶段,当间隙压缩到一定的程度,密度就相对比较恒定了,随着压力不断增大,密度也一样不会有太大的变化,因为颗粒之间的间隙已经到达极限,这阶段称为密度恒定阶段。当压力超过颗粒承受的范围就进入第三阶段,在这个阶段粉末颗粒会发生变形,颗粒与颗粒之间会紧密符合在一起,压坯的密度又随之增加,这个阶段主要是颗粒超过了可承受的领接点,发生了形变。
通常一个粉末冶金产品的毛坯密度分布,密度都是由中心向周围慢慢增大,粉末冶金产品的最上端的密度通常是最大的,越往下密度就逐渐减少,底部的密度就越小。原因就是受的压力不均匀导致密度不同,为了改善这一个原因,粉末冶金厂家将单向压制改为双向压制,尽管压坯的中间仍会出现密度比较低的区域,不过密度的整体分布有了明显的改善了。
前不久接了一个复杂的粉末冶金项目,由于粉末冶金产品的横截面复杂,但是又要保证整个粉末冶金产品的密度,否则在脱模后,密度不同的连接处就容易出现断裂和分层。粉末冶金毛坯的密度部均匀也会导致烧结过程中出现开裂的情况。为了使具有复杂横截面粉末冶金产品保持相同的压力与密度,必须设计多模冲压模,否则模具使用的寿命会非常短,比较有角的零部件,充填进去的粉没有地方均匀散去,就会在压力的状态下撑坏模具。
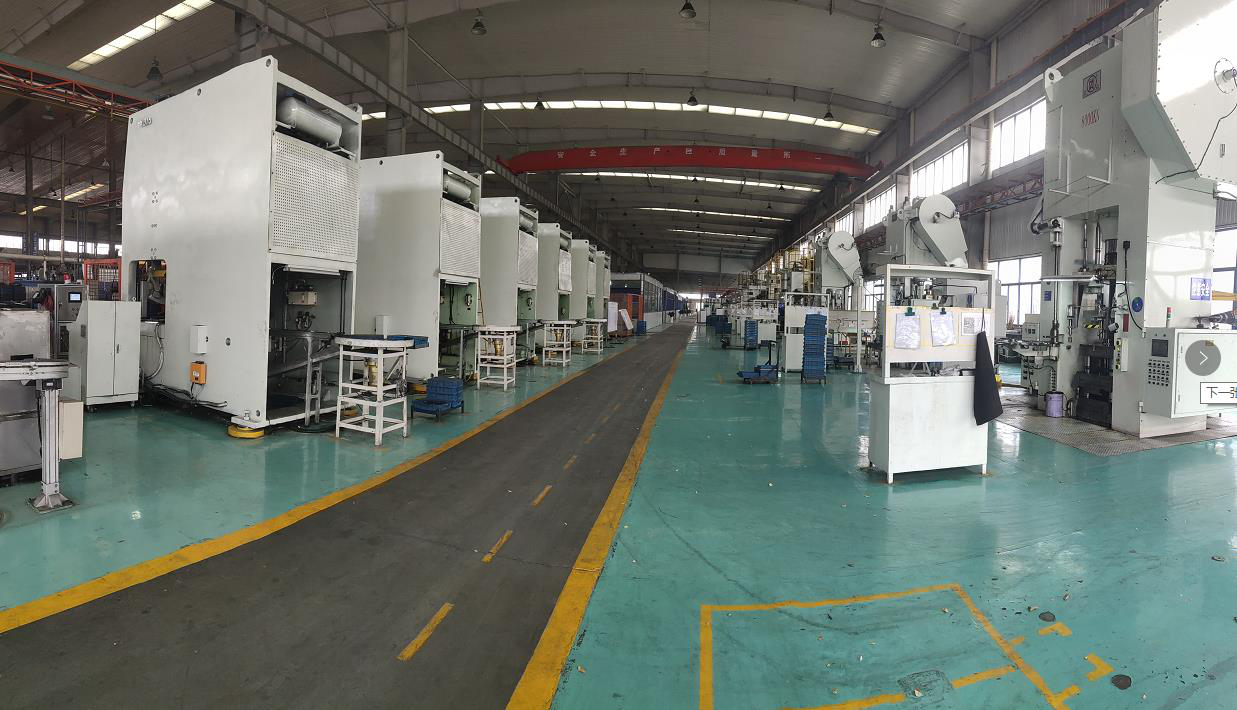