《MIM注射成型和常规粉末冶金PM哪个好》
形状复杂的零部件、尺寸较小、产量大等特点都成了粉末冶金的优势,粉末冶金常用的有MIM注射成形技术和粉末冶金压制两种。还有陶瓷注射成形,这里不做讲解。
很多人在粉末冶金常见两种工艺迷茫,不知道如何选择,这要根据产品的性能和形状来决定,连云港东睦新材料有限公司拥有这两项技术,可以很清晰看出适合的生产工艺。常规压制的粉末冶金产品,MIM注射成形基本都可以做,但是MIM注射成形能做的,粉末冶金常规不一定做。但是考虑到成本问题,合理选择更重要。目前粉末冶金技术使用在是手表行业、汽车行业、医疗行业、电动工具行业、军事行业都已经非常普及。
1.MIM注射成形和常规粉末冶金PM都能有效的缩减了切削工艺和机加工工艺,但是常规粉末冶金PM
只能做平面或三层以内,MIM注射成形可以实现几何图形,比粉末冶金压制更复杂的零部件。
2.MIM注射成型的产量比粉末冶金PM需要更大,对于一个小的零部件,注射成型可以一个模具生产8个、16个等零部件。所以用量低于5W件的很少使用注射成型工艺完成,但是也不绝对,如果客户能够接受价格的情况下,同样可以。
3.注射成型的密度高于粉末冶金压制,最大可以做到18.5,而粉末冶金压制大概也就是6.8-7.3之间。所以根据使用的粉末冶金产品性能来改变生产工艺。
4.注射成型可以对钛、不锈钢及镍合金之类难以切削加工的材料,一次性成型。如果含有这些成分的几何状零部件,常规粉末冶金PM做不了,那MIM可以做,越复杂的零部件,优势越明显。
5.MIM注射成形产品比常规PM粉末冶金产品表面的粗糙度要光滑的多,粗糙度最初反应就是粉末冶金颗粒的大小。
6.MIM注射成型给人一种感觉,生产的零部件都是偏小。其实注射成型也可以生产的大的零部件,只是原材料太贵了,比常规粉末冶金使用的原料高8倍以上。所以生产越大,用料越多,那么MIM工艺的优势越不明显。
7.注射成型在烧结过程中,缩的比例要比常规粉末冶金要大的多,所以把控这一块没有常规粉末冶金要好,烧结件的公差控制在±0.3%。
8.注射成形和粉末冶金共同的优势就是为了粉末冶金产品的性能更好,可以将粉末冶金件组合在一起,实现多个零部件成为一个零部件。
9.MIM产品比粉末冶金压制多一个缺陷,就是浇口,注射的位置需要灌料口,到时候需要后期初期,可以磨平,也可以做一个凹面。这个就不如粉末冶金压制了。
10.注射成形比粉末冶金压制使用的材料更广,可以实现新型组合材料,比如将金属和陶瓷材料混合在一起制作。
所以在不同的产品需求上,生产工艺可选性很多,但是粉末冶金工艺已非常适合现代化要求,经过几十年的发展,已经取代了很多铸件或是其他工艺的生产的零部件,今后在未来的零部件设计理念中,粉末冶金肯定会是设计者的首选。以上是连云港东睦新材料有限公司对MIM和粉末冶金的总结。(以下两张是连云港东睦新材料有限公司生产的粉末冶金产品和MIM注射成型产品)
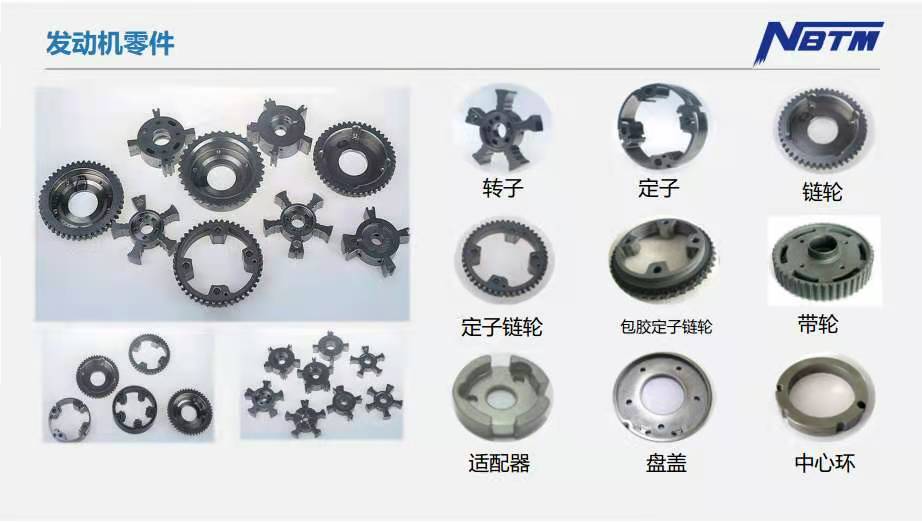
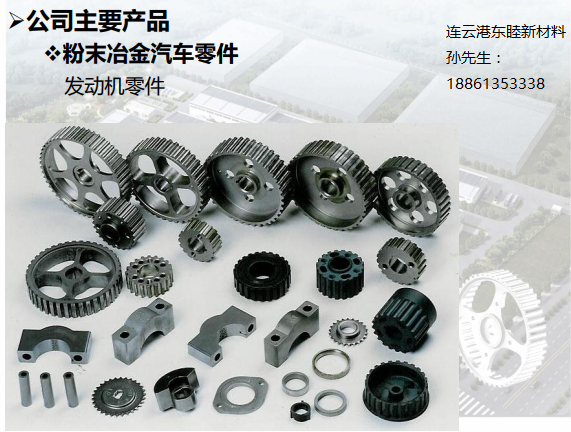
《常规粉末冶金压制与MIM注射成型哪个好》
目前制造的工艺种类很多,有锻造、压铸、冲压、熔模铸造、常规粉末冶金、MIM注射成形等,但是对于产品制造方式上选择考虑的因素很多。目的就是在完成需求的同时更大程度上节约生产成本。作为粉末冶金厂家工作的人员,今天分析的内容是适合于粉末冶金技术完成的零部件选择。
常见的粉末冶金工艺有压制PM和MIM注射成型,在这两样工艺上选择有上都有共同点,就是在建立一定数量需要的零部件上,因为粉末冶金都需要模具,由于流动性太大,粉末冶金厂家虽然不是以模具赚钱,但是对于潜力不大的客户,是不会承担模具费用,而是顾客自己承担,粉末冶金厂家直负责开发零部件模具,通常模具是用合金钢,原材料就好几百一公斤,一个模具大概需要几千到几万不等。收取模具费用是粉末冶金厂家寻求合作的保证金。有数量的基础上才可以考虑这项技术。
做为全球一家常规粉末冶金压制和MIM金属注射成形的两项技术同时超过10亿价值是东睦。东睦集团在连云港建设东睦新材料有限公司和连云港富驰智造科技有限公司,把粉末冶金PM压制技术和MIM注射成形技术综合在一起的生产基地,在产品工艺的选择上相互转换。(下面展示PM和MIM零部件图片)。
从零部件结构上分析适合的注射成形工艺还是压制成形工艺,首先是PM压制成形的零部件展示。
从连云港东睦新材料有限公司PM粉末冶金压制成形技术生产的零部件,我们可以看到基本都是二维平面状的零部件,那是因为PM压制成型取决于高压单轴压制成型,PM压制成型更适合于较为简单的结构件,一般角多的不太合适,形状复杂的零件,PM粉末冶金压制成形压制的密度会不均匀,所以说在有一定密度和强度要求的零部件,如果形状怪异就不太适合常规粉末冶金压制方法。正常密度能达到6.8-7.3之间,若是怪异形状的零部件则达不到,因为铁粉会将模具充爆裂,到时候粉末冶金厂家修模具都是一件比较头疼的事情,更不要说能够及时交货给客户了。(以下是连云港富驰智造科技有限公司)
从连云港富驰智造科技有限公司生产的零部件来看,零部件形状基本都是比较复杂的,在这一方面MIM注射成形件就没有形状的限制,三维立体几何形状的零部件在MIM技术来说是非常容易完成的。但是MIM注射成形的原料比常规粉末冶金压制使用的原料贵的多,接近于十倍的成本。使用的粉末非常的细,在4微米-20微米之间。生产的零部件偏向于小型几何图形的零部件。但是MIM本身若不是有原料成本的限制下,是可以制作大型的零部件,使用原料越多就越体现不出MIM注射成形的优势了。MIM注射成形零部件的精度比常规粉末冶金精度要高,机加工要少一点,原材料就节省很多,在产品性能上密度和强度都要超越于粉末冶金常规压制技术。
最理想的粉末冶金MIM注射成形产品
1.零部件的特征
(1)质量比较小,用料比较少,工艺复杂
(2)截面的厚度有变化,有截面厚度变化的产品别的粉末冶金压制就难制作,MIM比较适合
(3)壁厚大于0.1mm,小于10mm
(4)烧结时有一个支撑的平直表面
2.设计的特征
(1)轴对称、不对称、棱柱形、矩形及任意的几何形状
(2)加劲肋与组装的定位器特征
(3)悬臂与不对称形状
(4)伸出、凸起部和柱状螺旋
(5)根切、凹槽、狭槽、凹陷
(6)滚花表面与华夫表面
(7)用模具成形的零件编号或识别标记
3.注射成形不支持的特征
(1)尖角或棱边,圆角半径不低于0.05mm
(2)直径小于0.1mm的孔
(3)壁薄低于0.1mm
(4)没有脱模斜度的长形零件
4.注意尺寸的限制
MIM零件并不是生产小型零件,基于生产的成本考虑,比如生产大型件,使用的原材料多,有壁厚结构的零件,成本非常大搞,加上脱黏和烧结工艺的成本,就不能体现注射成形的优势,但是抛开这些因素,试验已证明零件质量最大为12-17kg,零件最长可以达到30mm,截面厚度达到125mm。
5.需要机加工的产品
后续需要大量机加工零件,有很多零部件形状非常复杂,不适合MIM件生产,但是MIM注射成形可以生成80%接近于成品,增加20%的机加工。在原料价格上,MIM件没办法和铸造件相比,因为原料贵很多,但是如果算上机加工费用,则是可以和铸造竞争的。
首先了解MIM金属注射成型的优势,MIM生产的基本是一个已经确定的成熟的零部件,采用注射成形MIM工艺生产的大多都形状复杂的零件。从零部件的4个点分析。
1.大小
通常使用MIM金属注射成型的零部件都比较小,重量控制在280克以内为最佳。这是因为一旦重量高了,使用的原材料的成本就高了。MIM金属注射成型制造的原材料的本钱远远高于常规压制PM粉末冶金原材料,除非是这个零部件非常复杂呈几何状只有MIM技术来完成。
2.复杂性
MIM金属注射成型的设计自由度和塑料注射成形零件相同。一个零件的几何形状越复杂,其用MIM工艺制造的合理性就越稳固。零部件可能有:横向孔、内螺纹、角度孔、不规则形状、根切、花键、侧向孔或沟槽、复杂形状或悬臂。或者在一些只有机加工完成的零部件上,MIM金属注射成型也可以制做出毛坯,减少机加工的费用。
3.最终性能
MIM金属注射成型件的优势在于高密度、高冲击韧性、断裂韧性、高疲劳、耐腐蚀性。对于难以切削加工的材料或者是高度加工的硬化材料,MIM工艺都是适用的。
4.产能
MIM件适合产能高的零部件生产,一般产能最少需要达到5万件左右,才能体现出MIM件的优势,若是没有,对于复杂的零部件,核算别的生产工艺的费用,MIM金属注射成型技术也是非常不错的选择。产量越高,性价比就会越高。
![]C82(H3RGDC3[Y6N2W93U1B.png](/upload/Pafb525a1099a4b21bcce88eeed192981.png)
![QNSL3QDPRA(1]{VXO{(}[ZS.png](/upload/Pc431f08a954b478c8d53c85d77a1da25.png)