不管是什么烧结过程,它都是粉末体的热固体结果。因此,广义上,烧结可以定义为松散的粉末或一定形状的粉末坯,在温度、压力、气氛的作用下,通过一系列化学、物理、冶金的变化,在粉末之间形成化学反映,成为致密固体的高结合体。
烧结过程中毛坯内发生的变化,无论是宏观还是微观,都很大程度上决定了最终产品的质量。下面将讨论与实际粉末冶金生产烧结过程中发生的尺寸变化的问题。
从宏观上看,烧结过程首先是烧结时毛坯体积收缩,即烧结体各方向的几何尺寸减少。当然,对于不同的化学成分体系,烧结时体积也会膨胀。但是,在大多数情况下,这是人们不期待的。
在粉末的实际烧结过程中,抑制烧结时压花尺寸的变化,即毛坯和烧结零件之间的尺寸差异是一个非常重要的参数。通常,毛坯和烧结零件的尺寸从平行和垂直于压缩的两个方向测量,以确定烧结收缩。经常会发现不同方向的尺寸收缩不同。这种收缩的各向异性与毛坯内残余应力的分布有关。
压制机工艺过程中最重要的几何尺寸变化是水平方向,即垂直于压力机方向的烧结体的尺寸和阴型尺寸的差异。这些差异是模具设计所需的核心数据之一。另外,还要注意压制过程的弹性后效果(即毛坯剥离后增加侧面尺寸)的影响。因为弹性后效果是线性膨胀的百分比,而测量的烧结体的尺寸收缩是克服弹性后包括效果膨胀在内的总收缩。另外,不良弹性后效与压缩压力成正比,实际上评价烧结收缩时需要注意多少压力。
另一个重要概念是毛坯密度和烧结体密度。它们都以质量和体积的比率表示为g/cm。烧结前后密度的变化主要由烧结时挤压尺寸的变化引起,但也影响质量的变化。润滑剂的挥发和粉末状颗粒表面的氧化物还原都会造成质量损失。
烧结体的收缩意味着毛坯密度的增加。单位制铜粉的烧结就是这样。影响收缩的因素首先是温度、粉末粒子的粒度,最后是成型失败时使用的压制压力。
实验中了解了纯铜粉压坯的收缩率与烧结温度及时间的关系,结果得知影响收缩性的最主要的是温度。例如,铜粉压胚在980度的温度环境烧结25分钟后,毛坯收缩性控制在11%,然后又将温度控制在750度,毛坯收缩控制在5%,从中得知温度对收缩性有很大影响。从25分钟延长到2小时,毛坯的收缩性从5%增加到6%,表明烧结时间的长度对毛坯的收缩性并没有多大影响。烧结温度的高低直接影响毛坯收缩性,同时我们得知烧结的收缩率在烧结初期(通常是前20min)大幅增加,随着烧结时间的延长而变平。总之,要想获得更高的烧结体密度,提高烧结温度比增加烧结时间更有效。粉末粒度也会影响烧结体的收缩。此外,还对865处粗粉(-105 75米)和细粉(-44um)压在压缩压力276MPa下的铜坯烧结后的烧结密度进行了比较试验。结果表明,微细粉末烧结体的致密化过程比粗粉末烧结体快得多,最终烧结体密度也比细粉末烧结体高。
影响烧结体致密化过程的一个重要因素是生化密度。也就是说,决定毛坯密度高低的是使用的压制压力,压制压力越高,毛坯密度和烧结体密度就越高。烧结体密度和毛坯密度的差异越小,烧结体收缩就越小。
一般来说,收缩是压制后和烧结后在室温下测量一定量的毛坯尺寸后计算的。用这种方法得到的数据是不连续的,更先进的方法是在烧结加热过程中持续测量一个样品的尺寸变化。这就是热膨胀仪的方法。使用热胀器,在特定加热速度下达到特定烧结温度保温时,可以记录样品大小变化的百分比和变化曲线,直接读取尺寸的收缩率,计算不同温度段的收缩率。
综上所述,单位制金属粉末毛坯后不是膨胀,而是在烧结过程中发生收缩。烧结体收缩受烧结温度、烧结时间、粉末粒度和压缩压力的影响。但是,大多数粉末冶金行业惯例,特别是烧结钢零件收缩率低于1%时,请选择尽可能小的烧结状态。收缩小的烧结状态对保持许多零件的尺寸一致性至关重要。
在其他粉末冶金零件的生产中,烧结体需要大幅度收缩以获得材料的理论密度。用细钨粉压制的毛坯密度为11G/CM’,在接近2分钟的温度下烧结后,线性收缩率约为15%,烧结体密度为18G/CM’,理论密度接近纯钨19.3G/CM’。然后,将烧结的钨经过旋转锻造和拉拔线。在这种情况下,不必精确控制烧结尺寸的变化。
需要注意的是,由比较柔软的金属粉末(如铜粉)制成的毛坯在烧结毛坯密度高的毛坯时,经常会发生烧结体体积膨胀。因为这种体积膨胀大部分是压缩过程中留在封闭空隙的气体,在烧结过程中引起体积膨胀,在气氛中保护氢气,使孔内表面氧化物产生的水蒸气无法逃脱。
对于较硬的粉末,由于毛坯密度低,烧结时孔仍然相连,不会发生这种现象。在比较柔软的金属粉末的低生不良密度毛坯上也没有发现体积膨胀的现象。
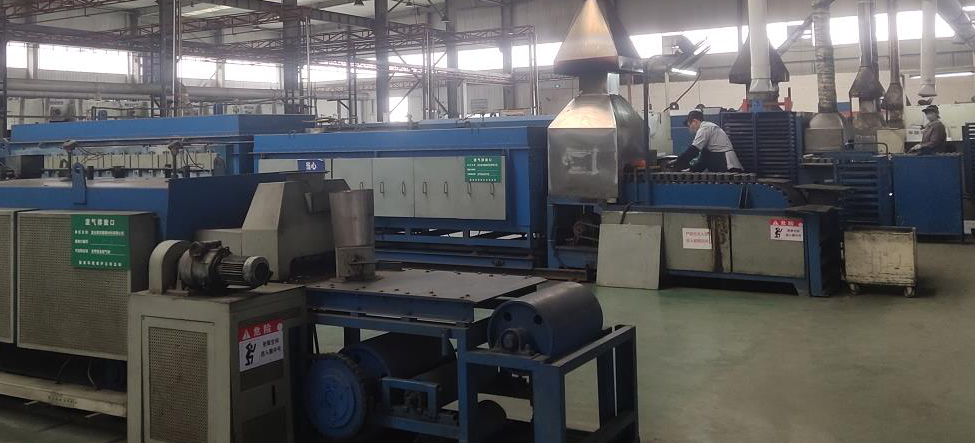
微观结构演化单元制金属材料(如铁)由微观组织构成晶粒网状组织。
用单元制金属粉末压制的显微组织也是如此。但是里面有很多大小和形状不同的洞。可以说是显微组织的第二相。下面是毛坯密度为6.5g/cm的铁粉压坯的情况,展示了微观组织从毛坯到完全烧结的毛坯的演化。未烧结的生压,微小的组织包围着毛坯的所有颗粒。因为压缩压力不足以填满粒子之间的所有间隙,所以可以看到粒子变形引起的更大的不规则间隙。在烧结的毛坯上可以看到仍然存在的大孔网隙,但孔是圆的。也就是说,材料移植将填充原始孔的末端。另一个区别是,原来粉末粒子周围的多孔缝隙消失了。也就是说,通过粒子系统的材料移动,粒子之间形成冶金连接,形成像退火锻造钢铁材料一样分割成晶界的晶粒网络。
单元制金属粉末毛坯显微组织的烧结过程的变化主要是指毛坯内孔的形状、数量和分布的变化。多元制金属粉末毛坯显微组织的变化除了孔的变化外,还代表着必要阶段的形成和发展。例如,烧结硬化过程中烧结钢的珠光体、贝氏体和马氏体的形成。
以单元制金属粉末坯料的烧结为例,烧结初期坯料中颗粒之间的点、线、小区域的接触会转变成线、带、大面积的接触,通过原子的扩散形成化学键组成的冶金结合,称为燃结接触颈。接下来,毛坯的原始连接孔或孔将被关闭。这是因为烧接触颈长大后不断被隔离连接孔隙。结果是,通过表面扩散,不规则孔的表面逐渐光滑,这些大大小小的孔发生体积收缩,大洞变小,小洞消失,结果是烧结体宏观体积收缩。这是我们期待的致密化阶段,在这个阶段,烧结的体内还有一定量的剩余孔,但大多数情况下,烧结体的材料性能可以满足使用要求。
如果不适当地继续延长烧结时间,气孔不会完全消失,只要总量不变,小气孔就会消失,大气孔会长大,气孔会变得粗糙。也就是说,原来分散的小气孔聚集在孤立的大气孔里。延长烧结时间后,出现烧结体力学性能明显下降的晶粒生长现象。为了了解气孔的形状、量和分布的变化,依次说明烧结初期(粒子形成实际接触,烧结的树木生长,气孔闭合,圆形)、烧结中期(气孔收缩,致密)、烧结后期(气孔厚度和晶粒生长)的微观组织变化。但是,必须提及的是,毛坯内部由不同厚度的粉末组成,因此粗粉之间的孔和细粉之间的孔变化速度不一致。总的来看,孔隙变化的这几个阶段并不完全同步,而是相互交叉。当不适当的烧结快速加热或进行其他工作时,微观组织变化可能会极度不平衡。特别是轮廓结构零件,如果内部有残余应力,则这些多种复合作用会使烧结体开裂,因此要避免。
在多元系金属粉被压下烧结的过程中,显微组织的变化除了气孔的动作与单位系金属粉相同的情况外,还有相结构的形成问题。相结构的形成具有一定的特殊性。以最简单的铁碳二元系为例,铁基结构最基本的成分是铁碳合金,铁是铁,碳是石墨,添加人。烧结过程中,部分石墨还原铁粉表面的微量氧化物,形成一氧化碳和二氧化碳,由于局部石墨过剩,往往以一氧化碳为主。活性一氧化碳中的碳原子渗透或扩散到铁的晶格中,随着量的增加,铁粒子逐渐形成铁-碳合金。这种相变的平衡成分可以根据铁一碳平衡图来预测。
但是,在烧结过程中,由于烧结气氛的影响,可能需要添加一定量的碳,以补偿第一次添加石墨等碳时可能出现的碳损失。因此,当铁碳合金的显微组织需要形成足够数量的珠光体时,要注意添加的石墨量与最终合金化碳含量的关系。在实际粉末冶金结构的生产中,控制孔往往通过压制达到足够的生态密度,而组织的上成分往往由合金的成分设计和实际烧结条件的调整来保证,两者都是同等重要的。