脱脂用反应堆不同。反映了粘结剂去除方法的多参数性。可供选择的炉子有真空炉、煤气炉、高压炉,用于加热脱纸和低压、高压溶剂脱纸。脱脂工艺取决于设备的工作方式,脱脂设备可以分为批次脱脂(间歇)和连续脱脂,脱脂用外资也可以用于烧结。根据脱脂方法,分为热脱脂、溶剂脱脂、虹吸脱脂、催化脱脂。在金属注射成型的实际生产中采用较多的石蜡基粘合剂体系,热脱脂是最常用、最重要的脱脂方法。催化剂脱脂是一种比较新和先进的脱脂方法,但对饲料有特殊的要求。下面重点介绍工业生产中常用的溶剂脱脂炉、热脱脂炉、催化剂脱脂炉。
一、溶剂脱脂装置
溶剂脱纸是将成型材料浸泡在至少能溶解一种粘合剂的液体或蒸汽溶剂中,过程反应器控制溶剂温度、循环和纯度,循环反复之前利用蒸馏附加装置从溶剂中排出粘合剂。形成连接的孔结构,促进后续粘结剂的去除。溶剂脱脂剂适用于含有两种以上元素的粘合剂。脱脂时先溶解其中一个,形成早期孔通道,不溶元素不溶解,保持MIM部件的形状。溶剂提取不能从成型的毛坯中去除所有粘合剂,所以最后一步要再次利用热量去除剩下的粘合剂。
溶剂脱脂装置由脱脂罐工作室、溶剂精馏塔、罐、加热温度控制系统等组成。将成型坯浸泡在装满溶剂的脱脂罐中,通过底部电阻器加热,水箱中的水达到一定温度,提高脱脂罐的溶剂温度,产生溶剂蒸汽,蒸汽从外部向内成型,推动层,溶解粘合剂中的石蜡元素,达到初步脱脂目的。溶剂被完全浸水破坏,该装置的溶剂及时净化,稳定净化温度,减少脱脂时产生裂纹等缺陷,因此,通常脱脂时间需要5个小时左右,使用石蜡作为粘合剂的MIM产品的热脱脂为热脱脂开辟了早期的孔通道,提高了热脱脂率,目前被广泛用于MIM产品的“溶剂脱脂和热脱脂”的脱脂工作中。
溶剂脱脂的效果可以通过测定成型坯的质量损失来判断。间隙溶剂脱脂系统除了脱脂环境是溶剂而不是气体外,与加热脱脂相似。
第二,用热的脱脂
热脱纸简单,容易控制,因此成为生产中首选的方法。加热脱脂可以在真空中进行,也可以在空气、氢、氮混合物、氢混合物或氮水混合物中进行。对于小分子如水的粘合剂,通常使用真空脱纸。空气是脱脂便宜有效的,但空气会氧化金属零部件,在烧结时引起相应的问题。氢是导热率高的分子物质,证明氢的这种属性有利于加热脱纸,但纯素的气氛容易引起爆炸,也不是分解聚合物分子的最佳选择。高温下,粘合剂或粉末中的残渣与氢气反应,形成气泡。脱脂过程中要控制气体的露点和碳。真空热脱纸的原理是,将注射毛坯从真空加热到粘结剂成分的挥发或分解温度,使粘结剂在热分解中发生物态变化,转变为气态物质,达到去除目的。温度低时粘结剂蒸气压低,实现部分蒸发去除。温度上升到粘结剂分解温度上方时,会发生分解反应,去除更多的粘合剂。大量热脱脂研究表明,热脱脂的关键是控制脱脂,在低温阶段(如150 ~ 350)缓慢加热(如1/MIN)不会引起变形或缺陷,因此真空脱脂炉的温度稳定性和均匀性良好。真空热脱纸比大气热脱纸真空压力低,更有利于粘结剂的挥发及分解产物的排放,因此脱纸率是比大气压力大的气氛脱纸。
由于生产率低,间隔工作不尽人意,但具有灵活性高、生产过程控制好的优点。因此,如果生产中的零件发生变化,间隔脱脂系统很有用。含有毛坯的炉子和气体的蒸馏室,包括控制时间、温度、压力和气体的控制器的间隔加热脱脂系统。成型毛坯的支撑上装有加热元件,可以准确控制温度。高级系统在气体出口配有许多传感器,用于检测反应产物气压,传感器中的信息用于提高温度或调节气体,以保持最佳脱脂率。系统内部安装了一台风扇,搅动了机身。气体入口和出口的位置要防止成型坯均匀地暴露在气体中,产生寒冷的部位。加热脱脂的部分产物是重分子,所以最好把出口设置在整形费下面。脱脂炉上工作负荷发生变化时,需要调整加热程序和气体流动速度,以确保均匀脱脂率,因此闭路反馈控制脱脂率是适当的控制方法。
另一种热脱脂形式是真空热脱脂。这是为了防止粘合剂进入真空泵,连续流动的保护气体,将气体粘合剂推入冷凝器中凝固的原理。由于保护气体的连续流动,内外保护区形成了小压差,实现了气体的单向流动,有效防止了脂肪物质污染发热体和内炉因压差过大而变形,实现了脱纸的目的。真空脱脂炉由以下五个部分组成:膨胀系统;加热系统冷却系统真空泵粘结剂收集器。
真空脱脂炉是MIM生产中最常用的脱脂器。目前广泛用于MIM铁基、不锈钢、硬质合金生产,可与溶剂脱脂剂一起使用。
三、连续催化脱脂
连续脱脂系统是时间、温度、气体(或溶剂)的相同组合,总脱脂基本相同,不同之处在于成型毛坯在通过一系列位置时不会阶段性传递。连续脱脂系统的优点是生产力高。
德国开发了快速催化脱脂技术。它使用多金属作为主要粘合剂,在含有硝酸的气氛中,将多金属从110度分解成甲醛气体。但是,这种脱气技术对脱气路要求高,固定投资大,需要耐酸脱气设备,设计炉具时要考虑环保问题,环境投资大。展示了催化脱脂炉的工作原理。也就是说,在110度 ~ 150度之间,以氮为保护气氛,将硝酸吹入使用多醛树脂为粘合剂的注射坯中,对多醛树脂产生催化分解反应,将生成的有害气体甲醛在高温的二级燃烧室中充分燃烧,迅速去除粘合剂。
为了去除粘结剂、去除剩余粘结剂、实现烧结过程之间的真正完全连续运行,德国克里默开发了“MIM-Mas-ter”催化剂脱脂和烧结系统。该系统包括连续催化脱脂炉和废气燃烧、气体对流干燥装置、旁路带、注酸系统、电气控制柜和包括全过程控制系统(PTC)在内的连续烧结炉和辅助装置。连续催化脱脂炉设计为使用Ni-Cr加热元件,工作温度为120度 ~ 140度 ,MIM零件放置在传送带上,预热带加热到100度以上。这样,通过可拆卸剂带时,酸不会凝结在工件上。去除粘合剂时,工件在载体(N2)和催化剂(经常是HNO3)的作用下去除粘合剂。炉子里气氛的流动方向很重要。在预热带,大气的流动方向与工作运动方向相同。直到进入尾气清除装置。在可拆卸剂带中,炉子的流动方向与工件的移动方向相反,并确保基本上去除粘合剂的零件能遇到最高浓度的酸。这个炉子的燃烧装置大小可能比同样生产力的布局炉小。这是因为废气在整个清除过程中连续发生,像放置炉一样,在一段时间内不会发生大量废气。燃烧装置设计成两级结构。第一阶段通向燃料气体、天然气等,与甲醛共同作用,在氧气不足的情况下燃烧,恢复NOx,剩下的HNO3还原乙。第二阶段,剩下的甲醛和燃料气体与过量的空气混合,产生二氧化碳和水。
MIM零件通过脱脂炉后,通过密封的横向传送带连续向烧结炉供应。零件需要在去除剩余粘合剂的烧结中避免振动,因此使用专门设计的步进梁传输机构。烧结路主要分为加热、烧结、冷却三个部分。温度上升段负责剩余粘合剂和预烧结作用,使用Ni-Cr线圈作为加热元件,最高工作温度800度。烧结带负责主要烧结作用,加热元件为Mo公司,最高工作温度为1450度。MIM部件在惰性或还原性气氛中烧结,生产中产生的废气在入口部分的排气烟囱燃烧后排出。冷却塔采用双壁水冷结构设计,可以手动调节冷却水流速和冷却水温度。MIM粘结剂的制备和去除是MIM的核心技术。MIM脱脂装置是低成本、大规模生产几何复杂、精度高、高性能接近最终形状产品优点的保证。热脱脂炉是石蜡粘结剂系统中最常用、最有效的脱脂剂,但要进一步提高热脱脂炉的温度控制精度和工艺稳定性及使用寿命。溶剂脱脂产品变形小,成品率高,溶剂脱脂可与热脱脂相结合,进一步提高脱脂效率。开发廉价高效的溶剂,提高容积利用率是开发溶剂脱脂设备的关键。催化脱脂炉可以用特殊的新型脱脂设备实现脱脂烧结的连续化,但只适用于特殊的等级和粘合剂。
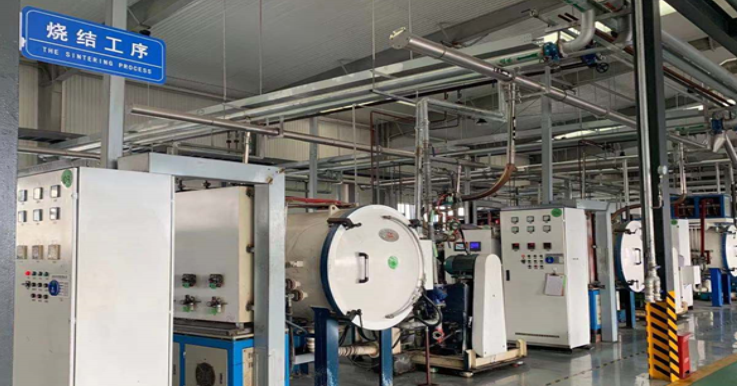